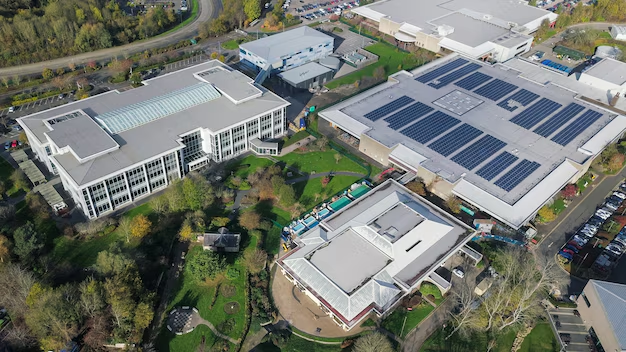
Energy efficiency has become a pressing concern across industries, and material processing is no exception. With rising energy costs, stricter environmental regulations, and the urgent need to achieve sustainability goals, material processing facilities are prioritizing innovative, energy-efficient solutions to stay competitive.
But why exactly are these solutions so important? This blog will touch on the vital role of energy-efficient practices in material processing, their long-term benefits, and the tools available to help companies meet these objectives.
Energy and Material Processing: A Challenging Relationship
Material processing industries like plastics, textiles, metals, and chemicals rely heavily on energy-intensive equipment and operations. High-temperature furnaces, heavy machinery, and advanced cleaning processes all require significant amounts of electricity or fuel, making these industries among the largest contributors to global energy consumption.
According to the International Energy Agency (IEA), industrial operations account for nearly 42% of global electricity consumption, with material processing playing a significant role. Energy use in this sector not only increases operational costs but also contributes to greenhouse gas emissions, placing additional pressure on facility managers to improve efficiency and sustainability.
Reducing wasteful energy practices can be difficult due to outdated equipment, production demands, and lack of technological integration. However, the cost of inaction—both environmental and financial—is far greater.
Why Energy Efficiency Matters in Material Processing
1. Cutting Operational Costs
Energy expenses are often among the largest overhead costs in manufacturing and material processing. By integrating energy-efficient technologies, companies can significantly reduce power usage while maintaining or even increasing production output.
For example, corona treatment equipment, which is often used to improve material adhesion in industries like packaging, can be optimized for energy efficiency to reduce unnecessary power consumption. Upgraded equipment not only saves energy but also helps maintain operational consistency, leading to fewer interruptions and higher yields.
Investments in energy-efficient solutions allow businesses to enhance profitability and even reinvest savings into further technological advancements.
2. Supporting Environmental Regulations and Sustainability Goals
Stricter government policies aiming to reduce carbon emissions have placed material processing facilities and manufacturers under the microscope. Regulations like the Energy Efficiency Directive in the European Union and compliance with the Paris Agreement push companies to limit environmental impact from their processes.
Energy-efficient solutions not only help companies maintain compliance but also play a role in achieving net-zero emission targets, which has become a core goal for many industries. Beyond compliance, adopting sustainable practices can also improve a company’s reputation and appeal to environmentally conscious clients and investors.
3. Improving Equipment Longevity and Performance
Energy-efficient machines tend to run cooler and with less strain compared to older, less-efficient counterparts. This can significantly improve the lifespan of industrial equipment. Additionally, advanced systems come with built-in diagnostics or sensors, allowing for better monitoring and predictive maintenance.
For example, by upgrading to variable speed drives (VSDs) for motors, manufacturers can ensure the machinery consumes only the necessary power, reducing wear and tear over time. Proper energy optimization ensures that material processing remains reliable, scalable, and sustainable.
4. Staying Ahead of the Competition
Industries that prioritize energy efficiency are often better equipped to innovate and adapt to market demands. With consumers and clients becoming more eco-conscious, adopting sustainable processes could be the differentiator between you and your competitors.
Imagine a textile company using advanced recycling technologies to reduce energy and water usage—they not only lower production costs but also meet consumer demand for greener products. This ability to align operational efficiency with market expectations often leads to better client retention and new business opportunities.
Practical Solutions to Optimize Energy Efficiency
Transitioning to energy-efficient solutions doesn’t require an all-or-nothing approach—it’s a scalable process that starts with smarter modifications. Here are some practical tips for businesses in material processing to consider today:
1. Invest in Modern Technology
Consider replacing outdated equipment with newer, energy-optimized machinery. Solutions like energy-efficient dryers, high-performance heaters, and advanced corona treatment equipment can significantly lower energy consumption while improving results.
2. Harness Data and Automation
Set up IoT devices or smart sensors to monitor energy use across your facility. Collecting data in real-time can help identify wasteful practices and optimize production schedules for greater efficiency.
3. Switch to Renewable Energy Sources
Where possible, invest in renewable energy options like solar, wind, or hydroelectric power as a supplement to grid electricity. Many processing facilities have successfully reduced emissions and energy costs through renewable integration.
4. Employee Training and Awareness
Energy-efficient systems are only as effective as the people who use them. Conduct employee training to raise awareness of energy-saving practices and encourage sustainable habits on the factory floor.
The Ripple Effect of Energy-Efficient Practices
Implementing energy-efficient solutions doesn’t just benefit the internal operations of a facility—it creates ripple effects across the entire supply chain. From reducing the carbon footprint of final products to building stronger relationships with clients and end-users, the ripple effect ensures that small changes can lead to larger, meaningful impacts at every stage of production and delivery.
By making these adjustments, you’re investing not only in the future of your company but also in the health of our planet. Businesses that lead the way in energy efficiency today will likely become the gold standard for the industry tomorrow.
The Time to Adapt is Now
The challenges facing the material processing sector today aren’t insurmountable, but they do require proactive, thoughtful changes. By investing in energy-efficient technologies, adopting smarter practices, and incorporating sustainability into every level of decision-making, companies can secure long-term profitability while contributing to a greener future.
Are you curious about how to make a difference today? Upgrading your facility with energy-optimized equipment, like corona treatment equipment, is a great start. Not only will this save energy, but it will also generate real results for your bottom line.
Proactive investments in energy efficiency are no longer just an option—they’re a necessity. Start evaluating your processes today and take the first step toward a more sustainable tomorrow.