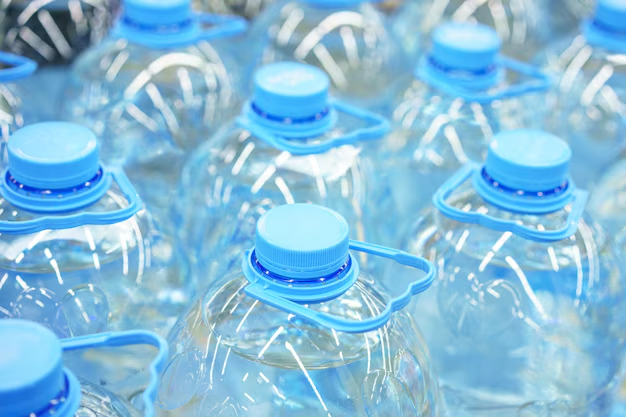
Efficiency is the lifeblood of manufacturing. Every second saved can enhance productivity, reduce costs, and improve profitability. One of the biggest culprits slowing down the production line? Long drying times. For industries reliant on adhesives, coatings, or printing, delays caused by waiting for materials to dry can pile up, causing bottlenecks and throwing off deadlines.
This blog will explore the effects of drying times on manufacturing processes, how faster drying can eliminate bottlenecks, and the technologies available to speed things up.
The Impact of Drying Times on Production
Drying times may seem like a small component of manufacturing, but they play a significant role in the overall production cycle. When every piece or component needs to go through a drying stage, waiting for curing can cause production hold-ups, creating bottlenecks that ripple throughout the manufacturing line.
Some common consequences of extended drying times include:
- Reduced throughput: Slower drying increases the intervals between completed batches, thereby lowering overall production output.
- Higher inventory costs: Materials that require longer drying and curing tend to occupy storage space, increasing on-site inventory expenses.
- Waste issues: Extended drying times can lead to defects if items don’t cure properly, wasting materials and creating rework.
For businesses striving to meet increasing demand, struggling with these challenges can hurt their ability to scale up or stay competitive. Faster drying times offer relief, enabling smoother operations and a seamless production process.
How Reduced Drying Times Boost Production Efficiency
Shortened drying times directly contribute to reducing delays and improving overall productivity. Here’s how:
1. Faster Line Speed
When products or components dry more quickly, manufacturing lines can maintain higher speeds without interruptions. This allows businesses to produce more units per hour or meet higher quotas in less time.
2. Minimized Storage Requirements
By reducing drying or curing time, materials move through storage areas and production lines faster. This limits the need for interim storage, freeing up space and reducing inventory costs.
Example Use Case:
A packaging facility switched to rapid curing technologies that cut drying time in half. As a result, the company eliminated the need for temporary holding bays, reducing operating costs significantly.
3. Improved Workflow Coordination
When drying delays are removed, it becomes easier to keep workflows synchronized across departments or production sections. Whether it’s applying a coating, assembling parts, or packaging finished products, faster drying allows various teams to collaborate smoothly.
4. Lower Energy Consumption
Traditional curing methods, like heat curing, can consume significant amounts of energy and add to operational costs. By transitioning to drying technologies that work faster and more efficiently, such as UV curing or infrared drying, manufacturers can save energy while improving throughput.
Technologies Enabling Faster Drying Times
Over the years, innovations in drying and curing technologies have revolutionized manufacturing processes. These solutions are designed to address speed limitations while maintaining the quality of the finished products.
UV Curing Systems
One of the most effective methods to achieve faster drying times is by using UV curing systems. These systems leverage ultraviolet light to cure and harden adhesives, coatings, and inks almost instantly. Industries such as printing, electronics, and packaging have heavily adopted UV curing due to its superior speed and performance.
For example, GEW UV curing systems for printing offer cutting-edge technology for manufacturers looking to enhance printing speeds while ensuring perfect curing. They are specifically designed to align with modern production speeds without compromising on quality.
Infrared Drying
Infrared (IR) drying systems use IR radiation to deliver rapid heat to materials, accelerating the evaporation of water or solvents. This is a highly efficient technique for industries such as textiles, coatings, and automotive.
Hot Air Drying Systems
While more traditional, hot air drying systems have evolved to incorporate efficiency improvements. Modern systems deliver controlled airflow and heat directly to components, reducing overall drying time.
Hybrid Solutions
Hybrid drying systems, which combine UV, infrared, and other technologies, offer manufacturers added flexibility to tailor drying speeds to specific materials or processes.
Reducing Bottlenecks to Scale Your Operations
For manufacturers aiming to scale their operations, reducing drying time isn’t just a nice-to-have; it’s essential. Faster processes naturally result in greater efficiency, but the benefits go far beyond operational speed. Streamlined drying processes can also enhance product quality, improve customer satisfaction, and lower defect rates over time.
Here are some practical ways manufacturers can start tackling bottlenecks caused by drying delays:
- Invest in Cutting-Edge Technology: Analyze your business needs and explore curing and drying technologies that integrate smoothly into your production line.
- Conduct Workflow Analysis: Look for inefficiencies within your current workflow that could be resolved by faster drying solutions.
- Train Your Team: Ensure your team is well-trained on any new drying technology to realize its full potential. Understand that efficiency gains depend on proper implementation as well as speed.
- Consult Experts: Partner with equipment providers or consultants to assess your specific bottlenecks and recommend tailored solutions.
Final Takeaway
Efficiency determines success in manufacturing. When bottlenecks related to drying times slow down production lines, businesses risk increased costs, customer dissatisfaction, and falling behind the competition. By upgrading to faster drying technologies like UV curing or infrared systems, you can significantly reduce delays, cut costs, and scale at a more competitive pace.
If your manufacturing process involves printing, adhesives, or coatings, why not explore GEW UV curing systems for printing to eliminate drying delays? Leveraging the right technology could be the key to unlocking your production line’s full efficiency potential.
Take the first step toward eliminating manufacturing bottlenecks today. Faster drying isn’t just a process improvement—it’s a competitive advantage.